Research & Development & Automation
of models, methods and workflows
Research & Development & Automation
of models, methods and workflows
We conduct direct numerical simulations — virtual experiments of the highest credibility — to gain deep insights into fluid flow and combustion processes. Leveraging the comprehensive data generated from these simulations, we develop advanced models for low-fidelity methods, enhancing their accuracy and predictive capabilities. Furthermore, we automate simulation workflows from geometry generation to post-processing and documentation, streamlining the entire process for efficiency and consistency. Our integrated approach not only accelerates development cycles but also provides you with reliable, data-driven insights to inform critical decisions. With expertise in computational fluid dynamics and process automation, we deliver solutions that optimize performance and drive innovation across your projects.
Our technology for your simulation workflow

CAD
CAD
Mesh
Mesh
Models
Models
Bondaries
Bondaries
Calculation
Calculation
Analysis
Analysis
The role of scripting and automation in CAD
The simulation perimeter is usually designed with CAD tools or simple parametrised design scripts. Here, the simplification of the domain is a balancing act between workflow efficiency and result falsification. This can be facilitated by specialised methods, which automatically reduce the feature resolution of your CAD-geometry to an appropriate level.
A further application for automation benefit is the geometry variation. It can be part of a product optimization process, or a AI-training process, or any other kind of parameter variation. Here, we couple the CAD control script with the CFD result analysis and perform a multidimensional optimisation according to the given requirements.
The following example illustrates a cooling channel with varying aspect ratios. By manipulating the height parameter, we can construct cooling channels with different aspect ratios. For each configuration, we compute the pressure drop in the cooling channel and the Nusselt number. These two parameters enable us to evaluate the overall efficiency of the cooling system. Subsequently, we can adjust the aspect ratio to optimize it, thereby identifying the most effective configuration in terms of efficiency.
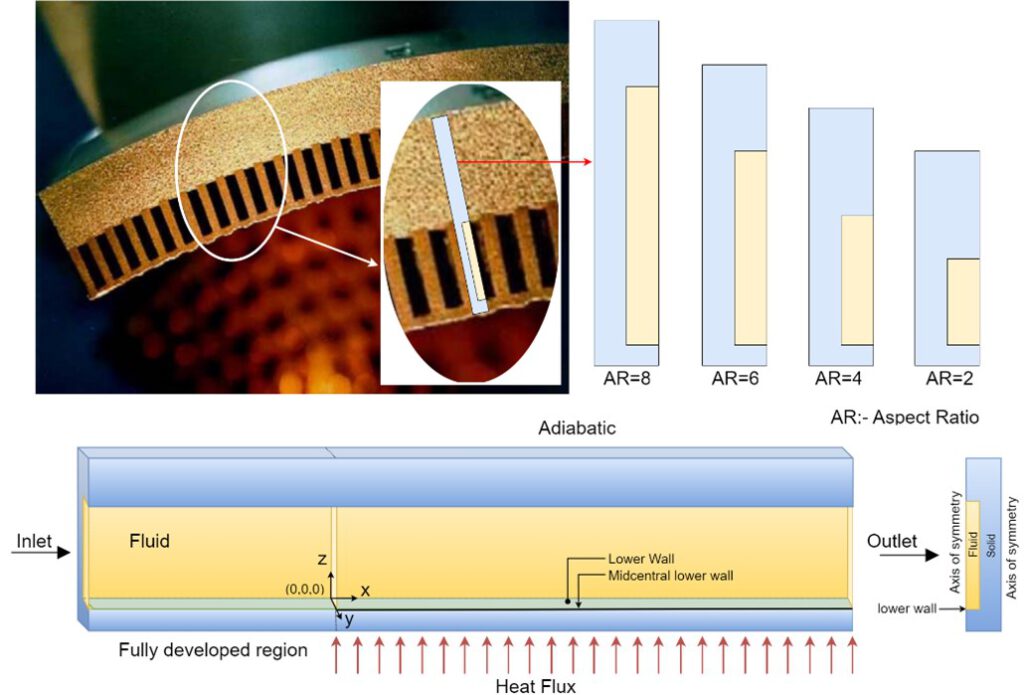
The role of scripting and automation in Meshing
We meticulously design our meshing strategies to account for a multitude of factors — including the simulation method and operating conditions — to ensure optimal accuracy and efficiency in your simulations. By employing advanced adaptive meshing techniques, part of the meshing process is dynamically conducted during the simulation, allowing the mesh to continuously adjust to evolving flow conditions for enhanced precision. Leveraging our extensive experience in numerical stability and mesh optimization, we can implement an automated workflow where the entire meshing process — from geometry generation to post-processing and documentation — is executed with minimal manual intervention. This automation not only streamlines your simulation workflows but also minimizes the potential for human error, accelerates development timelines, and ensures consistent, high-quality results.
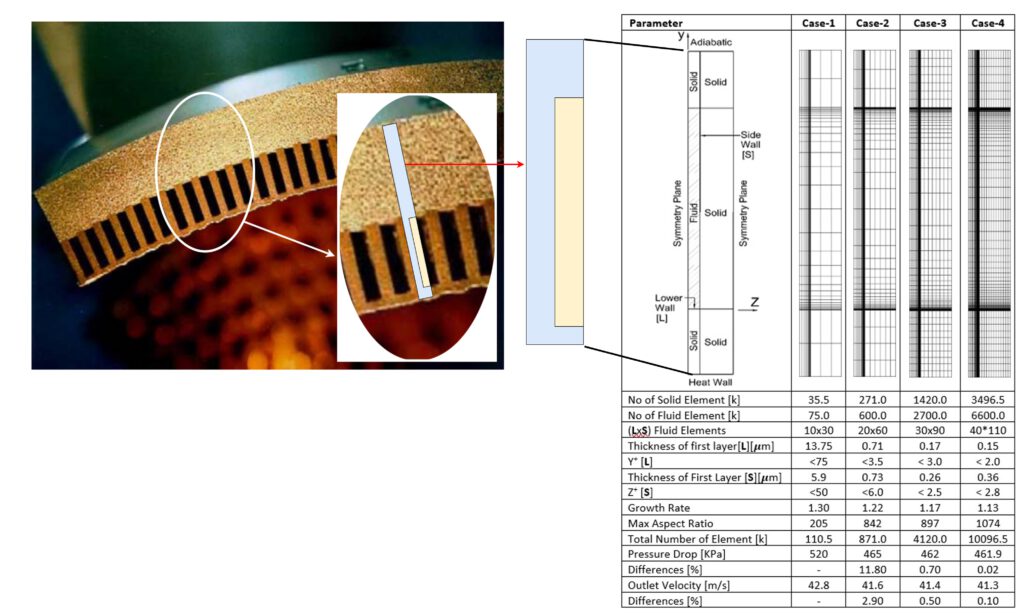
The importance of models
Selecting the appropriate models for all relevant physical processes is a highly intricate and nuanced endeavor. As your simulations incorporate a wider array of physical phenomena, the number of decisions regarding model selection and parameterization increases exponentially. Through our extensive research, we have identified interdependencies among many of these parameters. By understanding and leveraging these relationships, we can significantly reduce uncertainty and enhance the accuracy of our simulations.
Furthermore, we have advanced existing models by introducing new or adapted transport terms to encompass a broader spectrum of physical phenomena. Our team regularly employs direct numerical simulations (DNS) techniques to generate and analyze new data for the improvement of numerical models. This integrated approach not only refines model fidelity but also accelerates innovation in simulation methodologies.
Here is one example of how we used DNS simulations to derive a model for determination of molecular viscosity and Prandtl number (Pr) inside premixed flames. The picture shows show the values of Pr develop through the flame front.
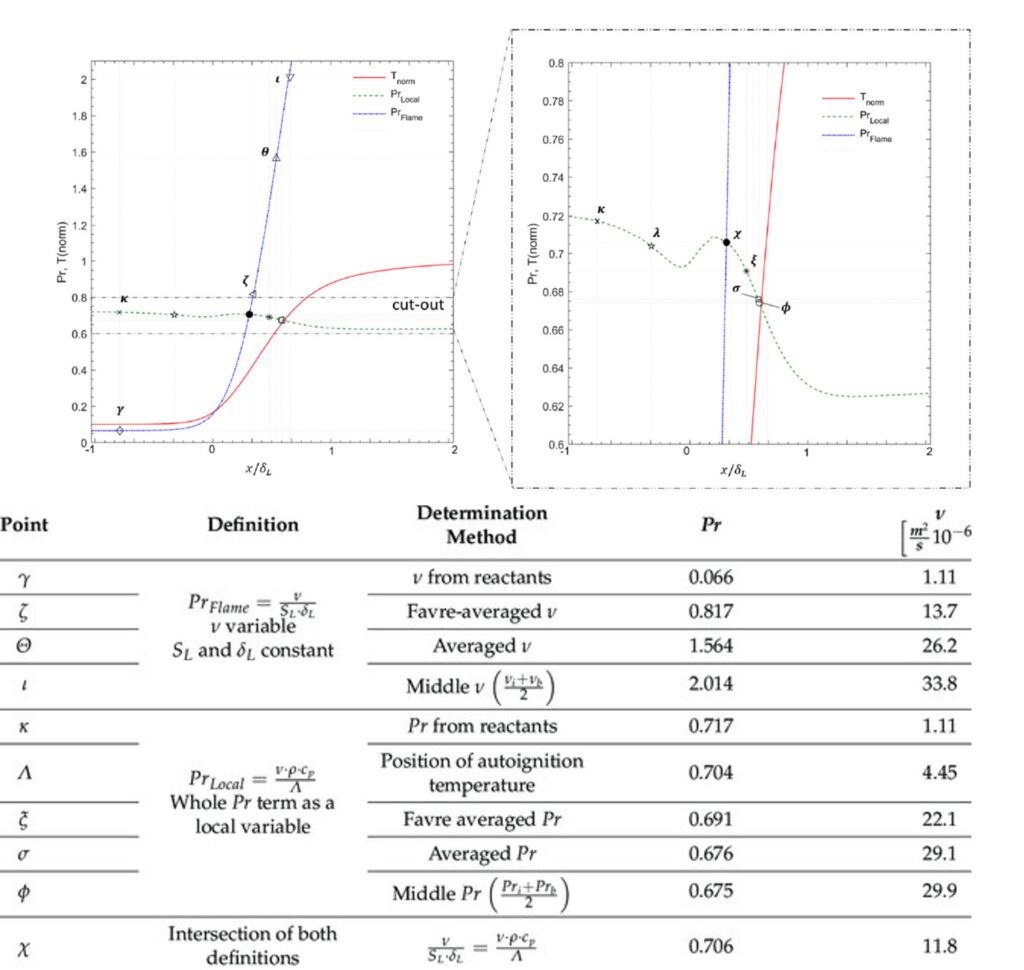
The challenge of boundary conditions
We incorporate detailed information about the system’s operating conditions directly into the simulation settings, typically utilizing simple scalar values for straightforward implementation. However, when boundary conditions are interdependent, vary over time, or are sensitive to internal physical fields, standard formulations may not suffice. In such complex scenarios, the creation of customized boundary condition formulations becomes necessary to accurately capture the system’s behavior.
Leveraging our extensive expertise in control technology and system automation, we can implement any specific requirements into the boundary conditions of your simulations. Our team is adept at developing dynamic, adaptive boundary conditions that respond to evolving internal and external factors. This capability ensures that your simulations remain accurate and reliable, even under intricate and variable operating scenarios.
In the shown example, we programmed a regulator for the stabilisation of a highly volatile turbulent flame front.
The hidden potential behind active calculation control
Traditionally, the computational simulation process requires you to predetermine critical parameters such as numerical schemes, convergence criteria, time steps, and total running time before initiating the simulation. This fixed approach can limit flexibility and may not account for evolving conditions within the simulation, potentially affecting both accuracy and efficiency.
We offer a dynamic solution where these settings are adjustable in real-time during the simulation. By implementing adaptive algorithms and control strategies, we enable the simulation parameters to automatically adjust in response to the evolving computational needs and physical behaviors observed. This adaptive methodology enhances the stability and quality of the results by optimizing settings on the fly.
Moreover, this approach can significantly conserve computational resources by allocating them more efficiently and avoiding unnecessary calculations. By tailoring simulation parameters dynamically, we achieve high-fidelity results while minimizing computational costs.
Our expertise in advanced numerical methods and real-time simulation control allows us to seamlessly integrate this adaptive framework into your workflows. By combining deep knowledge of computational physics with cutting-edge automation techniques, we help you achieve superior simulation outcomes that are both accurate and resource-efficient.
How to make postprocessing less annoying and more interesting
No matter how you intend to use your simulation results, streamlining the analysis workflow is essential for maximizing efficiency and productivity. If your daily responsibilities include regular documentation and reporting of simulation outcomes, we can equip you with customized visualization scripts that automatically generate all the necessary results.
For those conducting variation or parametric studies, you require more than just visualizing results—you need an additional layer of statistical analysis to interpret the vast amounts of generated data effectively. We offer advanced tools that extract only the relevant information from large data sets, analyzing and presenting it in various statistical formats. This enables you to uncover trends, correlations, and insights that might otherwise remain hidden.
Furthermore, we leverage cutting-edge machine learning methods to draw conclusions that can lead to improved simulation settings. By incorporating machine learning into your analysis workflow, we can help create an optimization loop that continually refines your simulation parameters for enhanced performance.
This very simple graphic is the result of a series of high-fidelity simulations which took a lot of effort and provided data in over a dozen dimensions. However by applying a series of automation algorythms a hideous analyis of all the data by hand was not necessary. Instead the system ran through all the data points, simulation cases and phsical fields by itself, filtered it and gave out a few best-practice recommendations about the most relevant correlations. Weeks of work has been reduced to a few hours. Automation is truly amazing.
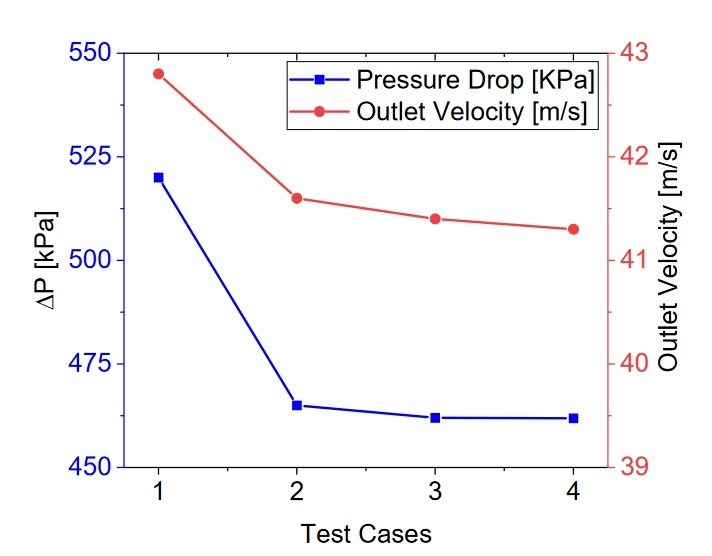